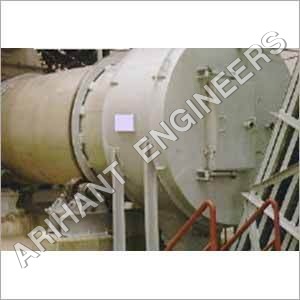
De Coater Plant
Get LatestPrice
Get Best Deals
De Coater ProcessDecoating is the process by which paint, ink, paper, plastic and oil are removed from the surface of a material usually metallic, to ...View Product Details
Product Overview
Key Features
De Coater ProcessDecoating is the process by which paint, ink, paper, plastic and oil are removed from the surface of a material usually metallic, to enhance recyclables. When coated scrap aluminum is melted directly in the furnace there will be substantial metal loss that will vary depending on many factors including.Type of coating:- Complex and multilayered coating can accelerate metal lossQuantity of coating:- As the quantity of coating present on the scrap increases than generally the amount of metal loss increases.The thickness of scrap:- Thin scrap exhibit a higher metal loss than thick scrap for the same percentage of coating.Normally UBC scrap contains 3 to 4 % of VOC compound by weight.Scrap preparationScrap preparation is most important for the decoating process. The presentation of scrap to the decoating kiln is very important for effective processing. Ideally the scrap feed should consist of individual pieces or shred having a large surface area /volume ratio. The pieces of scrap should be of a size and shape to facilitate transport in to the kiln without bridging or sticking. Typically pieces of about 25 -50 mm square are considered to be ideal.A large surface area is required to maximize gas/metal contact and so minimizing heating rate and reaction time.The reduction of as received scrap in to a form suitable for decoating is usually undertaken by shredding machine.The decoating processMore than 90 % of decoating is currently carried out in rotary kiln. The choice of rotary kiln is between parallel and the counter flow type. Hot gas flows through the kiln under controlled condition of temperature and oxygen content. The kiln exit gas containing evolved combustible is passed to an after burner and is combusted. A significant proportion of the combustion product is returned to the kiln for the processing, thus creating a recirculation loop. The most obvious choice is counter flow type kiln. In counter flow kiln the hot gases from the afterburner enters the kiln at the metal discharge end and flows counter to the scrap movement. This ensures the highest temperature and oxygen are in contact with the scrap exactly where it is needed. Consequently, counter flow kiln produce very good quality decoating. As the gas travels from discharge to charge end of the kiln there is an accompanying reduction in temperature. p { margin-bottom: 0.21cm; } The decoating process More than 90 % of decoating is currently carried out in rotary kiln. The choice of rotary kiln is between parallel and the counter flow type. Hot gas flows through the kiln under controlled condition of temperature and oxygen content. The kiln exit gas containing evolved combustible is passed to an after burner and is combusted. A significant proportion of the combustion product is returned to the kiln for the processing, thus creating a recirculation loop. The most obvious choice is counter flow type kiln. In counter flow kiln the hot gases from the afterburner enters the kiln at the metal discharge end and flows counter to the scrap movement. This ensures the highest temperature and oxygen are in contact with the scrap exactly where it is needed. Consequently, counter flow kiln produce very good quality decoating. As the gas travels from discharge to charge end of the kiln there is an accompanying reduction in temperature p { margin-bottom: 0.21cm; } excursion and removing the necessity for water sprays. Counter flow kiln do not require an internal refractory lining. The economics of decoating It is generally acknowledged that decoating will achieve higher recovery rates than non decoating systems. The main reasons for the increase in recovery are 1) Reduced melting time in furnace The faster a scrap is melted the lower the losses will be. 2) Cleaner materials charged in to the furnace It is well documented that the surface coating of a scrap has a profound effect on the subsequent melt loss. In general the higher the % coating the higher the losses will be. The effect differs between alloy types. For example, alloys with higher magnesium contents usually exhibit increased losses. Metal loss figures for UBC vary between 15-30 % for processes that do not decoat prior to melting. A well set up decoating and melting operation can limit metal loss to less than 10 %. This difference of about 5% can yield huge saving even for small user.
Company Details
Capitalizing on its state-of-the-art infrastructure and a pool of dynamic professionals, Arihant Engineers has established itself as a prominent manufacturer and supplier of Aluminium Melting Furnace, E-Waste Recycling Furnace, Hydraulic Tilting Furnace, Tilting Rotary Furnace and Horizontal Ingot Casting Machine. Used in the metal processing industries and recycling plants, these products are engineered using the best grade components and parts. Ever since we ventured into this business in 2007, we have been doing exceptionally well in terms of assuring quality of products and meeting delivery deadlines. We are able to achieve this feat consistently which has helped us build a strong market reputation of our company.
Business Type
Exporter, Manufacturer, Supplier
Employee Count
14
Establishment
2000
Working Days
Monday To Sunday
GST NO
24ABQPJ2589Q1ZR
Seller Details

ARIHANT ENGINEERS
GST
24ABQPJ2589Q1ZR
Proprietor
Mr N. C. Jain
Member Since
2 Years
Address
E-28, GIDC, Manjusar, Taluka Savli, Vadodara, Gujarat, 391775, India
Processing Machines & Equipment in VadodaraReport incorrect details
Related Products
Spices Processing Machines - Equipment Capacity: 1000 Kg/Day
Price - 1000000 INR (Approx.)
MOQ - 1 Set/Sets
LABH PROJECTS PVT. LTD.
Ahmedabad, Gujarat
More Products From This Seller
- Tradeindia
- Processing Machines & Equipment
- De Coater Plant In New Area
Recommended Products
Popular Products
Human HairForklift TrucksServo Voltage StabilizerBasmati RiceBackhoe LoaderCarry Bag Making MachineDrum LifterElectric StackerScissor LiftsIndustrial Vibrating ScreenRotameterFlowmeterRotary Air CompressorIndustrial Eto SterilizerRice Packaging MachinesShredding MachineHammer MillAutomatic Labelling MachineDiesel ForkliftAerial Work PlatformStorage Rack SystemEpoxy ResinMild Steel BarStainless Steel SheetsStainless Steel StripsBag Filling MachinesAsphalt PlantsSlat ConveyorOintment PlantPlanetary MixersLadies KurtisLed LightsCctv CameraBall ValveAnti Cancer MedicineAir CompressorIncense SticksSolar LightsGoods LiftsVitrified TilesStainless Steel CoilsPvc PipesPvc Pipe FittingsUpvc PipesUpvc Ball ValvePipe Elbows